Welcome, Guest |
You have to register before you can post on our site.
|
Forum Statistics |
» Members: 53,537
» Latest member: Bearviking
» Forum threads: 66,441
» Forum posts: 1,029,551
Full Statistics
|
Online Users |
There are currently 907 online users. » 22 Member(s) | 882 Guest(s) Google, Bing, Facebook, RobertW, msweig, med-one, boardmaker, harderhandyman, Tim in Indiana, jteneyck, fredhargis, cbop, Roly, mtl, ajkoontz, brnhornt, lincmercguy, firefighter, Bearviking
|
|
|
Chisel Handles: Minimum Complement of Tools Required |
Posted by: Philip1231 - 09-01-2013, 05:22 PM - Forum: Woodturning
- Replies (9)
|
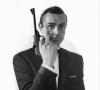 |
You'll probably get as many answers as there are turners, but this is what I use.
Any gouge to get it round and to rough shape. A skew for final shaping. A parting tool to cut it off from the waste. If you have the basic set from HF or Penn State that most of us start with you are good to go.
|
|
|
Work Smoother infill Build begins - need advice! |
Posted by: DallasStarter - 08-18-2013, 06:23 PM - Forum: Woodworking Hand Tools
- Replies (48)
|
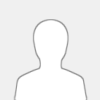 |
As we're presently in the process of trying to sell our house, I figured it couldn't really start a full-fledged piece of furniture as a next project. So, I decided to pull out the casting from Sturnella and begin work in earnest on this plane. To be honest, I was hoping someone else would post an excellent start-to-finish build-along before me so I'd have something to go on because I have zero experience making planes and only very minimal experience making tools (and certainly nothing as exacting as this!). So, when this turns out a wreck, at least we'll know why!
Anyway, I wanted to begin by preparing the casting. James was nice enough to mill the mouth a bit on the blade side, but he didn't or couldn't go all the way to the sides, so there's some file work to be done in both corners.
I don't have an special files for plane-making, but I knew I needed something thin enough to fit in the mouth, and ideally with a safe edge. Turns out an auger bit file works great as long as you don't have much material to use as was the case here. Still, it took some time, which was probably good to prevent me from overdoing it. Once I had it filed even all the way across, I found that the mouth still needed to be opened up along it's length to accommodate the hock blade. Not a big deal - just a little more file work, which was made easier to be sure by having a safe edge.
I then attempted to remove some of the small jagged irregularities from the pour of the casting - mostly just little guys the size of a large speck of sand, but too big across their base to just sheer off with some blunt force. I didn't have any files that had cutting action all the way out to the edge, so I ground the end of one on my grinder at about 85 degrees and with a slight convexity to allow focused efforts at scraping. This pretty much did the trick and I went about taking down the very high spots on the inside of the casting. The side walls are the easiest to do because you can come in with a small and rigid 120 sanding block after the initial scraping. I didn't get crazy with it, just enough to that the infills could slide in an maintain consistent contact with the sides vs. getting bound up on little rough or high areas.
Then I started thinking about design. I want this to have the general look of this Sauer and Steiner plane:
Which means overstuffed. As it comes out of the form, the casting has a roughish rounded edge all the way around. If I were to overstuff it now, there would be unsightly gaps all around where the infill met the bronze on the side. So, more filing:
Fortunately, I was able to use the high quality of the pour to my advantage. Since it was nice and parallel to the sole, I could file both sides at once in a cross-ways motion to ensure that I was approaching a flat that would also be square to the side. Then I did the rest:
I looked around for suitable infill material and found some mystery exotic that I'd bought at an estate sale a couple of year ago. I think it's rosewood, but really I have no idea. It is very heavy I will tell you that!
I also found some curly probably maple that would also work, but I think I'll probably go with the mystery wood.

Now on to the big questions. What bed angle to shoot for? The angle machined into the bed is about 47.5 degrees. I'm all set with smoothers at 45 and 55 degrees. So should I go even higher? This template was drawn up for 58.5 but perhaps I should go for 60? Or maybe I should calm down and go for 50 (an intermediate angle I don't have)?
Also, do we think there's enough room down there for shavings to be pulled out? How do people feel about the prospective position of the pins for the lever cap? Do I need to worry about leaving more meat around (and especially above) it?
I appreciate everyone's thoughts - especially those of you who have and use infills or especially those who have built them!
Reed
|
|
|
Chipbreaker success |
Posted by: Wilbur Pan - 07-24-2013, 06:27 AM - Forum: Woodworking Hand Tools
- Replies (12)
|
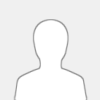 |
Wilbur thanks for this post. I've seen videos from Japan that would bear out what you say. Chipbreakers are particularly helpful when planing against the grain or with complicated grain. The study concluded that they aren't as necessary if you are able to plain with the grain.
On western planes, chipbreakers can help stiffen the normally relatively thin blades (quite unlike Japanese kanna) and minimize chatter, or so I've read here on the forum.
I expect that this post will have quite a few replies before the day is out.
|
|
|
How to polish a saw plate |
Posted by: Christian Castillo - 05-08-2013, 01:53 AM - Forum: Woodworking Hand Tools
- Replies (166)
|
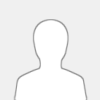 |
Hi, a few months ago I saw a beautiful saw restored by Daryl Weir in a post here, he did mention he used no sandpaper or machines, with those two hints I set off to see if I could find a way to replicate his results. My saw plate polishing method is performed with the following steps, although step 1 may be omitted if the saw plate has light rust/tarnishing and the rust issue isn't severe as step 2 can actually cut through a lot of rust on its own. I just jumped straight to step 2 because my saw didn't have a lot of rusty build-up.
Disclaimer: Wear gloves, the ball of foil will chew up your skin.
1. Use a razor blade or something similar to scrape off as much rust as you can off the saw plate.
2. Use a high quality metal polish ( Autosol, Flitz etc. ) and dab it onto the saw plate, no need to waste a lot, you can literally just bang the tube of polish against the plate in key areas so that you will have enough polish to do the job. Now get some Aluminum foil, crumple it up into a ball and begin scrubbing the plate until you literally clean the polish off the plate. You will understand what I mean as you keep scrubbing, eventually the aluminum foil will clean up the plate and take all the polish off as if it is wiping it clean. If there are some areas that could use more polishing, just dab some more metal polish on and keep working until you are satisfied.
That is it, this method is incredibly clean since you do not have dirty mineral spirits or water and steel sloshing around and staining everything near it. The saw plate will literally clean itself and if you are careful, you many not even dirty your hands. The foil is too soft to abrade the saw plate, but is hard enough to scrub away the rust. The polish will then brighten and clean the plate making it very smooth and reflective, perfect qualities for a hand saw. I love this method because you do not introduce new abrasion marks into an old tool and I feel it achieves results faster, cleaner all while retaining the marks of age and history, I'm done going through a grit progression of sand paper, I'll save grit progression for sharpening.
Excuse the quality of the pictures, I took them about an hour and a half ago outside. It took me 20 minutes to finish the one side of this saw, I'm going to polish up the side with the etch tomorrow, it's late and dark but if you see how the plates shine in the day light, its really something.
 IMG_2555 by Christian Castillo1, on Flickr
 IMG_2556 by Christian Castillo1, on Flickr
 IMG_2558 by Christian Castillo1, on Flickr
|
|
|
|